Waterproof Flex PCB with Coating and Potting
- Flex Plus Tech team
- 7 days ago
- 4 min read
Flexible PCBs are known for being small, bendable, and easy to fit into tight spaces. But recently, another important feature has become more and more important—waterproof flex PCB performance.
Contrary to common belief, the base material of a flexible PCB is already waterproof.
As the base material for most flexible circuit boards, PI (polyimide) inherently possesses water resistance. However, to achieve the functionality of a fully waterproof flexible printed circuit board, it is not only dependent on the bare board, but also on the components, connectors, and surface protection measures within it. These factors collectively determine the final level of waterproofing.
Here, we’ll clarify what a waterproof flex PCB really is, how different waterproofing methods work, and how to design your flex PCB assembly to meet IPX3 through IPX8 waterproofing standards.
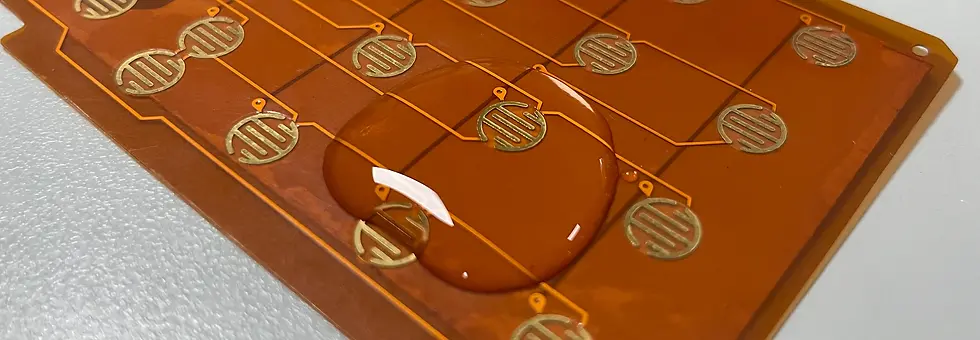
Is flexible PCB Itself Waterproof?
The answer is yes. This flexible circuit board composed of polyimide, copper and coating features inherent moisture-proof properties. The reason for choosing these materials is that they possess excellent electrical, thermal and environmental stability.
So, in its raw form, an flexible PCB is already a waterproof flex PCB.
However, once you begin mounting components, exposing solder joints, or using connectors, the integrity of that waterproof protection can be compromised. That’s where coating and potting come into play.
Where Waterproofing Is Needed
To make a complete waterproof flex PCB assembly, focus protection on these areas:
Surface-mounted components
Exposed solder joints or pads
Vias or plated through-holes
Connectors or interface terminals
Edge connectors or exposed circuits
Waterproofing treatments must be applied to these zones to ensure moisture doesn’t compromise the circuit.
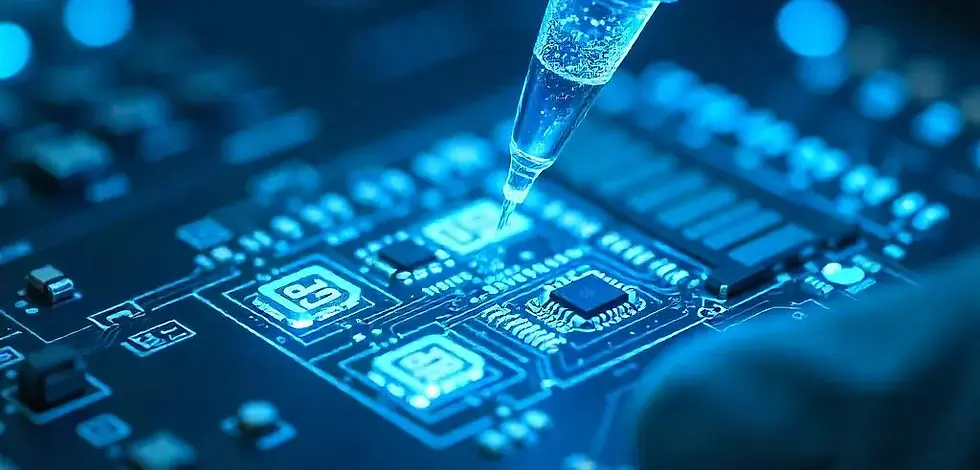
Two Waterproofing Methods: Coating vs. Potting
1. Conformal Coating (Up to IPX3)
Conformal coating is a light, protective layer applied over the entire flexible PCB surface to guard against moisture, dust, and minor splashes.
Common Coatings: Acrylic, silicone, urethane
Application Ways: Spray, dip, or selective coating
Waterproof Rating: Typically up to IPX3 (protection from water spray)
Advantages: Lightweight, cost-effective, preserves flexibility
Limitations: Not suitable for immersion or continuous water exposure
While conformal coating offers a basic level of protection, it’s not a complete solution for waterproof flex PCB applications in wet or submerged environments.
2. Encapsulation or Potting (Up to IPX8)
Potting (also known as encapsulation) involves fully covering sensitive areas—or even the entire circuit—in a protective waterproof compound.
Materials Used: Epoxy, silicone, polyurethane
Waterproof Rating: Up to IPX8 (protection from long-term immersion)
Applications: Wearables, automotive sensors, marine equipment
Advantages: Robust, long-lasting protection from water and chemicals
Limitations: Adds weight and thickness; reduces flexibility in sealed areas
For full submersion protection, potting is the most reliable solution to achieve a true IPX8 waterproof flex PCB.
How to Design for Waterproof Flex PCB Performance
Creating a reliable waterproof flex PCB solution starts with smart design. Here are practical tips:
Use Protective Coating or Potting Zones
Identify zones that need waterproofing (e.g., solder joints, ICs, sensors) and apply selective coating or potting while keeping flexible areas exposed for bending.
Minimize Component Density in Flex Areas
Keep critical components in rigid or reinforced sections. This allows potting or sealing without impacting the bending capability of the flex zones.
Select IP-Rated Connectors
Choose waterproof connectors to maintain sealing integrity. Many IP67 or IP68-rated connectors are available specifically for flex circuit assemblies.
Design Enclosures with Waterproofing in Mind
Sometimes, the waterproof flex PCB is only part of the solution—the product housing may provide mechanical sealing to meet IPX5 or higher ratings.
Applications of Waterproof Flex PCB
With proper surface protection, waterproof flex PCBs are ideal for a wide range of applications:
Smart wearables – Fitness trackers, smart bands
Automotive electronics – TPMS, headlights, cameras
Medical devices – Portable monitors, skin-contact sensors
Industrial sensors – HVAC monitors, remote data loggers
Marine equipment – Underwater lighting, GPS trackers
These devices demand compact, flexible, and moisture-resistant circuitry, which makes waterproof flex PCB solutions an ideal choice.
Common Waterproofing Standards Explained
IP Rating | Protection |
IPX3 | Water spray at up to 60° angle |
IPX5 | Low-pressure water jets from any angle |
IPX7 | Temporary immersion (up to 1m depth) |
IPX8 | Continuous immersion (>1m, as specified) |
Achieving IPX8 requires careful integration of sealing, potting, and often enclosure-level protection. We help you select the best approach for your specific application and cost targets.
Why Work with Us for Waterproof Flex PCB Projects?
We’re a professional manufacturer of flexible PCB and rigid-flex PCBs with strong experience in waterproof circuit solutions. Our production capabilities include:
✅ In-house conformal coating and potting lines
✅ Support for both low and high-volume orders
✅ Advanced testing for IPX3–IPX8 compliance
✅ Quick turnaround and DFM guidance
Whether you need simple splash protection or full submersion sealing, we help bring your waterproof flex PCB project to market faster—with confidence.
Contact us for a free quote or consultation
Conclusion
The term "waterproof flexible printed circuit board" may cause confusion unless we delve into the issue from the perspective of the pure circuit material. Although the flexible circuit board itself has some moisture-proof properties, the true waterproof effect depends on the protection methods of the components and interfaces. Coatings can provide basic protection, but to achieve a level of protection like IPX7 or IPX8, encapsulation is indispensable.
By combining reasonable design with appropriate waterproofing methods, you can create electronic devices that can operate normally even in the harshest environments.
Let us help you make your flexible circuits waterproof—effectively and affordably.
Comments